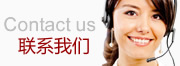
電話:0371-55682180
傳真:0371-55682180
手機:136-7371-1977
郵箱:3489671897@qq.com
地址:鄭州新密市超化鎮(zhèn)工業(yè)園區(qū)
配合料在電弧爐中經過熔化和精煉階段后達到澆鑄標準以后,將將熔融液由電爐直接澆入鑄型的操作過程稱為澆鑄。此過程雖然短暫,但每一步都關系到最后產品的質量,是一個復雜的工藝階段。這里只介紹一下我國熔鑄耐火磚常用的幾種方法:
1.澆鑄的方法
1.1普通澆鑄法(代號:中國PT,康寧、旭、東芝RC,西普RN):鑄件采用普通的冒口澆鑄,并在熱態(tài)時鏟除冒口,其斷面分為兩個部分,一部分先固化,結晶細密,該區(qū)占鑄件厚度的40%-50%,另一部分后固化,存在縮孔和粗大結晶。用這種方法澆鑄的磚價格較低,多用于窯的上部結構,澄清池壁等處。
1.2傾斜澆鑄法(代號:中國QX,康寧TA、旭TC、東芝TCL,西普RO):傾斜澆鑄法是在澆鑄之前將鑄型造成一個角度,并將冒口放到鑄型的一端進行澆鑄,這樣既能在T部得到一個致密區(qū),又可利用普通模具在T方向上得到較高的精確度。所以用這種鑄件砌筑池壁時,便可利用它的高度。
1.3無縮孔澆鑄(代號:中國WS,康寧VF、旭VF、東芝DCL,澆鑄,將縮孔集中在某一區(qū)域內,退火后用金剛石鋸把他切除,剩余的有用部分成分均勻,組織致密,其平均體積密度接近理論密度;另一種是切割鑄腿法:從減少切割面積出發(fā),將鑄件澆鑄成“L”型,使縮孔的絕大部分集中在“L”較小的腿上,此腿體積占鑄件總體積的60%,整個鑄件在退火時一直埋在保溫材料里,并保持傾斜以促使縮孔向腿上集中。這種工藝由于切割代價高-金剛石鋸切割費用一般都高于鑄件本體的價格,顧只有在個別情況下采用。
2.澆鑄過程的特征
澆鑄過程,對鑄件質量有很大的影響,不僅影響鑄件外形的完整,而且還直接影響到鑄件內部的質量。澆鑄過程的特征如下:
1)在澆鑄過程中,熔融液與鑄型之間進行著劇烈的熱交換過程和化學反應過程。澆鑄時熔融液溫度很高,與鑄型之間有很大的溫差,所以澆鑄過程中,熔融液不斷冷卻,溫度降低,而鑄型被加熱,鑄型材料組成物分解氣化,與熔融液進行某些化學反應,使型腔內氣壓增加,對充型不利。嚴重時會出現(xiàn)漲型,是鑄件有氣孔層或澆鑄不足等缺陷。
2)熔融液澆鑄過程是不穩(wěn)定的過程,澆鑄流股的沖擊和流量的不勻等,嚴重時會使鑄件產生鼓包、冷隔、鑄口所在面空殼等缺陷。
3)熔融液充填砂型的過程,相似于充填多孔容器,因為砂型壁有一定的透氣性,如果型腔內的壓力低于型壁內的氣壓,則熔體會吸入外界氣體造成氣孔等缺陷,反之,熔融液會被壓入型壁孔隙中,造成嚴重附砂。
4)澆鑄過程的時間長短對鑄件的溫度分布有顯著影響。
3.澆鑄工藝
澆鑄工藝包括澆鑄溫度、澆鑄速度、澆鑄時間和補澆3.1澆鑄溫度
澆鑄溫度是爐內熔液澆入鑄型時的溫度,一般是用光學高溫計測量靠近爐嘴處的流股溫度。AZS磚強化熔融時,澆鑄溫度可達1820-1840度。熔體的黏度取決于熔體的化學成分和溫度,而熔體的組分決定于配方,因而溫度起重要作用,熔體的溫度越高,其黏度越低,因而流動性越好,充型能力越強。但并非澆鑄溫度越高越好,如果澆鑄溫度過高,使鑄件與模型之間的溫差減小,由表向里的凝固區(qū)的寬度增大,凝固收縮速度加快。在收縮應力增大的同時,初期晶粒粗化,成分偏析,在鑄件的核心部位最后凝固時極易產生熱裂,大二后的鑄件更是如此的。因此應根據(jù)鑄件的大小及形狀規(guī)定一個澆鑄溫度上限,防止開裂,同時還要規(guī)定一個下限防止充型能力不足。
3.2澆鑄速度和澆鑄時間
澆鑄速度決定了澆鑄時間。沒個鑄件都有最佳澆鑄時間,澆鑄時間不當會使逐漸產生很多缺陷。如果澆鑄速度過快則流股粗,流速快,對鑄模的沖擊力大,鑄模的一部分被沖破或熔融,是該部分鑄件產生突起。此外,粗大的熔體快速澆入鑄模時,一部分氣體被帶入鑄模中并迅速上升到模型的頂蓋。此時,接觸頂蓋的熔體已形成薄殼,在薄殼下充滿氣體,形成所謂的空殼。同時,帶入的氣體也容易在鑄型中形成氣泡。除了氣體以外,高速澆入的粗大流股還可能將爐嘴區(qū)的生料帶入熔體內,在熔體中形成夾雜。相反,如果澆鑄速度太慢,也會產生諸如邊角疏松、節(jié)疤、夾砂以及澆不足等缺陷。當澆注速度慢,流股很細時,先澆入模型中的熔體凝固成小球,充至邊角,造成邊角疏松。如果先澆入的熔體已凝固成薄殼,向內收縮。后澆入的熔體進入到薄殼與模型之間的縫隙內形成表面疤痕。
同時,如果流股太細,熔體在為達到邊角時已凝固,造成澆不足。而且,由于澆鑄的時間過長,模蓋的烘烤時間過長,易剝落掉入熔體中造成夾砂。
3.3補澆
鑄件澆鑄完畢,冷縮一段時間后,在其出現(xiàn)的縮孔里再鑄滿熔液,這一操作過程成為補澆。通常小型磚凝固很快,不能補澆,中型磚可以補澆,間隔時間較短,只有大型磚補澆時間較長。補澆是減小鑄件縮孔,提高容重的有效手段之一,它實際上相當于擴大了冒口的容積,操作的關鍵在于控制補澆的最適宜時間。實現(xiàn)連續(xù)的多次補澆是提高產品容重的重要方法。
4.澆鑄與澆鑄中氣孔的關系
普通澆注的AZS耐火磚有縮孔和縮松存在是正?,F(xiàn)象,但是經常發(fā)現(xiàn)有很多氣孔存在,顯然,任何一個氣孔的存在都會直接降低鑄件的質量。
鑄件中的氣孔有兩類,一類是顯微氣孔,只有制成薄片在顯微鏡下才能看到;另一類是宏觀氣孔,肉眼可見,也就是我們常說的氣孔。他們不外來自四個方面:即爐料、熔化過程、鑄型材料、澆鑄過程。
這里就鑄型和澆鑄對氣孔的影響進行討論。
4.1由鑄型材料引發(fā)的氣孔
和鑄型接觸的鑄件邊緣,常見的氣孔有兩種:
1)垂直于型壁而密集的皮下蜂窩狀氣孔是由于砂型工作面潮濕引起的。水是發(fā)氣物質,一個單位體積的水被加熱到1000度變成水蒸氣,在壓力保持不變時體積增大1700倍。如果加熱到澆鑄溫度,可能要達到近萬倍。所以砂型表面上的水突然生成這么多的氣體將形成一個高壓,使氣體侵入正在凝固的邊緣熔體,并向阻力小的方向延伸,于是變成了長條形狀。因此,澆鑄操作中,禁止使用潮濕的鑄型。
2)皮下圓形氣孔,多是離邊緣10毫米以內的單個圓形氣泡,這是由于砂型粘接劑在與熔體接觸時分解產生大量的氣體,一部分從砂型空隙逸出,一部分由于瞬時型腔排氣不暢,壓力而侵入熔體,所以澆鑄時注意型腔排氣是很重要的,當然提高砂型的透氣性(例如用圓形砂粒清洗沙中塵土,背面的透氣性要大于工作面的等等),是指從里向外不斷擴大更為重要。
4.2由澆鑄操作引發(fā)的氣孔
這類氣孔有三種:澆鑄口面空殼、泡沫層內部針孔等。
4.2.1空殼
快速澆鑄時,型腔排氣不暢,于是在磚頂面死角處形成氣袋,凝固后,即成為只有一層薄殼的大面積氣袋層,在廢品分析中稱之為空殼。為了防止空殼的形成,所以澆鑄操作除了時間限定外,還具體提要求澆鑄流股先粗后細,先快后慢。但在接近充滿型時,必須適當快一點,否則上邊角會出現(xiàn)澆不足,而型蓋為避免被熔體形成的靜壓頂開,都要壓上重物或人力壓住。
4.2.2泡沫層
鑄型內落入保溫材料等雜物,與落入型腔的第一段熔液反應生成一個僵化的氣泡層,浮于液面上,一直上浮到型腔頂面,凝固后形成鑄口面的氣泡層,故澆鑄前必須檢查并保持型腔清潔。
4.2.3針孔
針孔往往發(fā)生于澆鑄的第一塊磚,這是因為爐嘴區(qū)沒有清理干凈,混有生料或石墨爐嘴氧化露頭粉末等,與熔液急劇反應后澆入鑄型,由于熔液黏度大,這些氣泡不能上浮,便不規(guī)則的留在熔液里。所以澆鑄時保持熔液通道的清潔也是不能忽視的。其他條件引發(fā)的氣孔最常見的是爐料潮濕和熔融溫度不足,使鑄件成為縮孔分散型或稱面包型。此外還有不被人們注意的操作,例如(1)澆鑄前串動了電極,使大量石墨粉落入爐內,結果造成在鑄件夾雜氣孔而不致密;(2)帶電澆鑄,在電極同熔液繼續(xù)反應的情況下料液是不致密的,顯然鑄件也不會致密;(3)帶生料澆鑄,特別是爐口前區(qū)有生料時澆鑄,生料進入鑄件,除破壞巖相結構外,也產生氣孔。
5.澆鑄過程中的缺陷及防治措施
5.1澆鑄過程中的缺陷
5.1.2鑄件的收縮
鑄件形成縮孔、縮松、內應力、裂紋、變形等缺陷都與熔液凝固時發(fā)生的收縮有關。鑄件的收縮可分為液態(tài)收縮、凝固收縮、固態(tài)收縮三個階段。對固定成分的AZS來說,其液相線溫度是個常數(shù),因此澆鑄溫度越高,液態(tài)體積收縮就越大。凝固收縮則表現(xiàn)為型腔內液面的繼續(xù)下降,所以凝固收縮加上液態(tài)收縮,就是鑄件產生縮孔的基本原因。由此比重差已知AZS這部分的體積收縮可達12%-15%。
5.1.3鑄件中縮孔的形成及其影響因素
縮孔的形成:熔融液在鑄型內發(fā)生自型壁開始逐層凝固時,如果由液態(tài)收縮和固態(tài)收縮引起的熔液減少,得不到補充,在鑄件最后凝固的地方就會出現(xiàn)集中縮孔。
當鑄件邊緣溫度降到固相線溫度以下時,鑄件表面變形成一層硬殼,形成一個包著溶液的密封容器。當進一步冷卻時,殼內熔液一方面因溫度繼續(xù)降低發(fā)生液態(tài)收縮,另一方面由于硬殼增厚而產生凝固收縮,這兩者的收縮因得不到補充而使液面降低。另外,固態(tài)殼同樣因溫度降低而發(fā)生固態(tài)收縮,使鑄件外表尺寸縮小。由于AZS熔液的液態(tài)收縮和凝固收縮都大大超過外殼的固態(tài)收縮,所以在重力作用下,頁面將與外殼的頂面脫離,出現(xiàn)縮孔。隨著凝固繼續(xù)進行,硬殼不斷加厚,液面將不斷下降,待熔液全部凝固后,在鑄件的鑄口下方,核心部分就形成一個縮孔。
如果硬殼內的溶液中氣體量少,那么當液面和殼頂面脫離時,縮孔就形成真空,上表面的薄殼在大氣壓力作用下就可能向縮孔方向凹陷進去,此時的縮孔就應包括外面的縮凹和內部的縮孔兩個部分。
影響縮孔體積的因素包括:熔液本身收縮大,則縮孔容積大;熔液本身凝固收縮大,則縮孔體積大;熔液本身固態(tài)收縮大,則縮孔容積減小;澆鑄速度越緩慢,縮孔體積就越小;鑄型的激冷能力越大,縮孔體積越小。
5.2鑄件中縮松的形成及其影響因素
縮松是指鑄件縮孔的下方,分散的細小空洞或密集的粗晶,或粗大的結晶群體等,肉眼能看到的都稱為縮松??s松的形成主要與熔液成分,結晶凝固特點以及鑄件的凝固順序有關,當鑄件結晶性很強時,在最后凝固的縮孔處變自由的生長出粗大的結晶,AZS這部分往往是粗大的柱狀剛玉晶體,晶面上長有六邊形的斜鋯石晶體。當細長的鑄件周邊凝固,熔液補縮困難時,其下部便產生軸線縮松。
5.3減少鑄件縮松和縮孔的基本方法
制定合理的澆鑄工藝來有效的控制凝固過程,建立良好的補縮條件,盡可能的使縮松轉化為集中縮孔,使它移向鑄件最后凝固的地方,這樣就可以在其上加一個冒口,使縮孔最后移入冒口內,從而獲得致密的制品。
凝固過程分為順序凝固和逐層凝固兩種方式:所謂控制凝固過程就是把自然的逐層凝固(表面層先凝固,逐漸向鑄件中心長厚)人為的從鑄件遠離冒口的末端區(qū)到冒口之間,建立一個逐漸遞增的溫度梯度,使末端區(qū)先凝固,然后按順序向著冒口方向凝固,即實現(xiàn)順序凝固,以達到熔液補縮,將縮孔引入冒口的目的。順序凝固,容易使鑄件不同部位,存在較大溫差,從而使鑄件出現(xiàn)裂紋和殘留應力等缺陷的傾向。
5.4冒口
5.4.1冒口的作用及其補縮原理
對鑄件凝固收縮進行補給的非鑄體本體的附加部分稱為冒口。冒口有減小縮孔和排氣以及做觀察孔的作用。冒口的大小、形狀、數(shù)量,必須保證他是凝固最慢的部分,并有足夠的容積,容納足夠的熔液,以補充鑄件在凝固過程中發(fā)生的體積收縮。
冒口補縮的基本原理:鑄件在凝固的過程中必須存在一個朝向冒口的溫度梯度,當鑄件冒口區(qū)和末端區(qū)是彼此連接時,便可獲得無縮孔的致密鑄件。反之,冒口區(qū)和末端區(qū)之間,被一個無溫度梯度的中間區(qū)隔開,則中間區(qū)將出現(xiàn)軸線縮松。
5.4.2冒口的設計
冒口設計的內容為形狀、尺寸和數(shù)量以及處置方法。
1)冒口形狀
根據(jù)冒口補縮原理,冒口必須是最慢凝固的部分,因此設計冒口時,首先要求他散熱速度小,其形狀應在相同體積下具有最小表面積時熱量散失就慢。計算表明:球體的表面積最小,然后是圓柱體、立方體、依次遞增。冒口設計還需考慮實際生產中制作的難易,所以在AZS生產中不用球形冒口。
2)冒口尺寸
主要是指它的直徑和高度,由于鑄件形狀復雜,大小不一,其所需冒口不能相同。因此引入一個補縮模數(shù)即冒口體積與鑄件體積之比,以控制鑄件單重為目標來選取冒口的大小。大容積的冒口對提高鑄件容重是有效的,大容積冒口分為一個大冒口或兩個中冒口,或一個冒口用完之后再更換一個冒口等多種形式。
關于冒口的高度,一般認為冒口越高,液體靜壓越大,補縮作用也越明顯。實際上,如果冒口過高便會抵擋不住熔體靜壓而發(fā)生外凸,同事鑄件底部退火后有裂紋,所以在不改進其它的工藝條件下片面的提高冒口高度是不可取的。根據(jù)AZS的縮孔縮松占有澆鑄高度一半的規(guī)律,認為冒口高度的設計原則應是與鑄件的高度一致,即二者之比為1:1。
3)冒口的數(shù)量及處置方法
一般一個鑄件選用一個冒口,普通澆鑄中鑄件長在700毫米以上者則選用兩個冒口,冒口的處置方法有兩種:冷割除和熱鏟除。冷割除冒口:當冒口連同鑄件在一起退火,則冒口的鏟除必須用用金剛石鋸片切割。熱鏟除冒口:鑄件澆鑄完畢后,等待冒口補縮結束后立即將冒口除掉,并用砂型板蓋上鑄口,然后退火。熱鏟除冒口的時間控制是很重要的,過早則冒口作用減小,熔液外溢,鑄口凸起增大冷加工量:反之過晚,鑄件易產生內裂,故根據(jù)磚型大小,冒口的大小,一般控制這段時間為12-40分鐘,保持鑄口面略低于鑄件表面且平整美觀。
上一篇:RTO蓄熱式焚燒技術簡介
下一篇:加入這個可提高致密耐火澆注料的抗渣侵蝕性能
- 水泥回轉窯的這幾個特殊部位,是耐火材料砌筑的關鍵 2023-12-09
- 澆注料、搗打料等不定形耐材的施工要點 2023-12-09
- 耐火磚的堆放技巧 2023-12-09
- 煉鋼用耐火材料 2023-12-09
- 教你耐火磚濕法砌筑的施工技巧 2023-12-09
- 玻璃池窯各部位所用耐火材料的應用情況分析 2023-12-09
- 陶瓷窯爐施工應注意的問題 2023-12-09
- 碳化硅的合成及碳化硅耐火材料的性能及用途 2023-12-09
- 煉鐵高爐內襯結構和原理 2023-12-09
- 沖天爐用耐火磚及澆注料類型 2023-12-09