編輯:
admin
分類:耐火知識(shí)
發(fā)布:2022-12-02 17:31:54
瀏覽:次
致密耐火澆注料發(fā)展的趨勢(shì)是要求鋁酸鈣水泥含量盡量降低,同時(shí)保持較好的生坯強(qiáng)度和高溫力學(xué)性能,其中關(guān)鍵的技術(shù)在于提高顆粒間的堆積密度。通過(guò)微粉、亞微粉甚至納米氧化鋁粉體的加入,可有效實(shí)現(xiàn)上述目的,其原因有:
1)降低了澆注料中CaO含量,減小高溫下生成的低熔相,能顯著提高澆注料的高溫力學(xué)性能;2)促進(jìn)中溫下的燒結(jié),增加澆注料的中溫強(qiáng)度;綜合性價(jià)比,氧化鋁微粉的作用不容忽視,其顆粒形貌、大小、粒度分布和比表面積等都會(huì)對(duì)澆注料性能產(chǎn)生較大影響,尤其是粒度分布對(duì)填充骨料間孔隙、提高堆積密度起著重要作用。研究發(fā)現(xiàn):使用不同粒度分布的復(fù)合微粉能顯著提高堆積密度,減少用水量,對(duì)力學(xué)性能如高溫抗折和熱震后強(qiáng)度有利。李文平等研究了氧化鋁微粉粒度對(duì)澆注料性能的影響,發(fā)現(xiàn)隨著微粉粒度的降低,澆注料流動(dòng)性和凝結(jié)時(shí)間均呈現(xiàn)增加的趨勢(shì)。更為重要的是,氧化鋁微粉能夠促進(jìn)鋁酸鈣水泥高溫下CA6相的生成反應(yīng),從而對(duì)澆注料高溫性能改善的作用明顯。Pinto等發(fā)現(xiàn),氧化鋁微粉粒度的降低,可使含1%(質(zhì)量分?jǐn)?shù))CAC水泥的澆注料的抗折強(qiáng)度提高近一倍以上,且能促進(jìn)CA6相的生成。Auvray等發(fā)現(xiàn)氧化鋁微粉優(yōu)化和CA6的原位生成,在澆注料中可形成陶瓷結(jié)合,顯著改善澆注料的高溫彈性模量。基于實(shí)驗(yàn)室球磨制備的氧化鋁微粉,研究其含量對(duì)澆注料物理性能、高溫抗熔體侵蝕等的作用機(jī)理,以探討澆注料中微粉的適宜添加量。采用板狀剛玉顆粒和細(xì)粉為主要原料,其Al2O3含量大于99.0%。顆粒的組成為:5~3mm占20%,3~1mm占20%,1.000~0.088mm占28%。小于0.088mm的板狀剛玉細(xì)粉和自制氧化鋁微粉(Al2O3含量>99.5%)總比例為28%,具體組成如表1所示。自制Al2O3微粉的粒度指標(biāo)如下:D10為0.43μm,D50為2.82μm,D90為9.27μm,比表面積為5.88m2/g。結(jié)合劑鋁酸鈣水泥的含量為5%,醚基聚羧酸脂(FS10)分散劑的含量為0.15%。制備過(guò)程為配料、干混攪拌5min、加水濕混3min、澆注振動(dòng)成型。樣品尺寸為40mm×40mm×160mm,加水量控制在6%以下。成型后的試樣在模具中自然養(yǎng)護(hù)24h,然后脫模在空氣中養(yǎng)護(hù)24h,再在110℃干燥24h,最后將試樣在1100、1600℃分別保溫3h進(jìn)行熱處理。

表1澆注料的試驗(yàn)配比
采用排水法測(cè)量試樣的顯氣孔率和體積密度,對(duì)應(yīng)的國(guó)家標(biāo)準(zhǔn)為GB/T2997—2000。采用三點(diǎn)彎曲法測(cè)量試樣的常溫抗折強(qiáng)度,設(shè)備型號(hào)為TIRAtest2820,跨距125mm,加載速率0.15MPa/s,對(duì)應(yīng)國(guó)標(biāo)為GB/T3001—2007。高溫抗折強(qiáng)度(HMOR)采用國(guó)標(biāo)GB/T3002—2004進(jìn)行測(cè)試,設(shè)備型號(hào)為GD–1,跨距和加載速率等參數(shù)與CMOR測(cè)試相同。試樣的熱震穩(wěn)定性采用水冷法測(cè)試,條件為室溫~1100℃,保溫30min,熱循環(huán)次數(shù)為3次,用殘余耐壓強(qiáng)度來(lái)衡量試樣的熱震穩(wěn)定性。采用感應(yīng)爐動(dòng)態(tài)抗渣試驗(yàn)來(lái)評(píng)價(jià)試樣的抗渣侵蝕性,將試樣鑲嵌在坩堝爐襯中,坩堝底部放入2kg鋼塊,上面覆蓋堿度為4.2的鋼包渣500g;鋼塊完全融化到抗渣試驗(yàn)結(jié)束,總時(shí)間為30min,鋼渣的成分為:CaO46.46%、SiO214.15%、Al2O32.10%、MgO4.93%、Fe2O325.49%、MnO2.45%、K2O0.16%、Na2O0.62%??乖囼?yàn)完成后對(duì)試樣進(jìn)行顯微結(jié)構(gòu)分析,所用設(shè)備為NovaNanoSem400型場(chǎng)發(fā)射掃描電子顯微鏡。2.1微粉含量對(duì)剛玉質(zhì)澆注料常溫性能的影響制備試樣時(shí)的加水量和流動(dòng)值如表2所示。由表2可以看出:隨著氧化鋁微粉含量的增加,剛玉細(xì)粉含量的減少,配料所需的加水量隨之減少、澆注料的流動(dòng)值相應(yīng)增大;當(dāng)微粉加入量為10%(試樣A),加水量為5.86%,流動(dòng)值為190mm;當(dāng)氧化鋁微粉加入量增大到22%(試樣D)時(shí),加水量減少至4.64%,流動(dòng)值也增加至240mm。原因是相對(duì)于剛玉細(xì)粉,氧化鋁微粉能夠更好的填充大、中、小顆粒間的氣孔,排擠出氣孔中的水;微粉含量的增加,在良好分散條件下會(huì)明顯提高澆注料的致密化程度,從而降低其加水量。
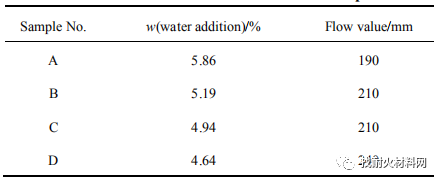
表2 澆注料試樣A~D的加水量和流動(dòng)值
試樣經(jīng)110℃保溫24h、1100℃保溫3h和1600℃保溫3h熱處理后的AP和BD變化如圖1所示。從圖1可以看出,隨著氧化鋁微粉加入量從10%(試樣A)增加至22%(試樣D)、剛玉細(xì)粉相應(yīng)的從18%減小到6%時(shí),經(jīng)不同溫度熱處理試樣的顯氣孔率呈減少的趨勢(shì),1600℃熱處理后試樣顯氣孔率從19.9%降低至15.8%,體積密度相應(yīng)增加,從3.03到3.20g/cm3。
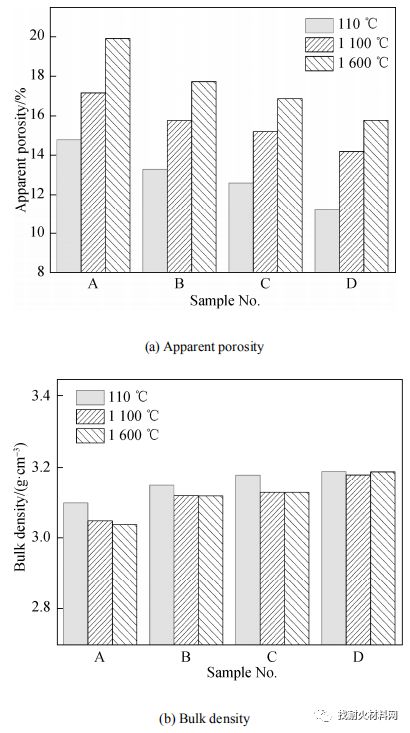
圖1試樣的顯氣孔率和體積密度
經(jīng)不同溫度熱處理后試樣的常溫抗折強(qiáng)度(CMOR)隨微粉含量的變化如圖2所示。隨著氧化鋁微粉加入量從10%(試樣A)依次增加至22%(試樣D)、剛玉細(xì)粉相應(yīng)的從18%減少到6%時(shí),經(jīng)110、1100和1600℃熱處理后試樣的常溫抗折強(qiáng)度均有不同程度的增加。當(dāng)溫度為110℃時(shí),強(qiáng)度由8.40MPa增加至13.56MPa,增幅為61.4%;當(dāng)溫度升高至1100℃時(shí),強(qiáng)度從5.04MPa增加至8.03MPa,增幅為59.3%;當(dāng)熱處理溫度達(dá)到1600℃時(shí),試樣的強(qiáng)度從27.15MPa增加至41.77MPa,增幅為53.9%。
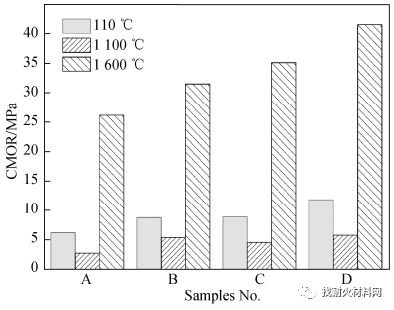
圖2 試樣的常溫抗折強(qiáng)度
氧化鋁微粉能夠減少澆注料的氣孔率,提高其體積密度,這對(duì)試樣強(qiáng)度的提高有利;另一方面,微粉具有促進(jìn)燒結(jié)的作用,加入量越多,試樣基質(zhì)部分的燒結(jié)越充分。文獻(xiàn)表明微粉越細(xì)越有利于燒結(jié)。燒結(jié)理論擴(kuò)散傳質(zhì)動(dòng)力學(xué)公式為:
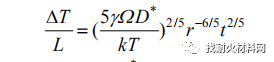
其中:γ、?、D*、k、T、r和t分別為表面張力、原子體積、自擴(kuò)散系數(shù)、Boltzmann常數(shù)、溫度、顆粒尺寸和時(shí)間。由此理論結(jié)合澆注料的級(jí)配知識(shí)可知,在主要由大顆粒組成的澆注料中,在質(zhì)量分?jǐn)?shù)<30%范圍內(nèi)加入的微粉越多,所制成的試樣燒結(jié)越充分,致密化程度越高,力學(xué)性能越優(yōu)良。2.2微粉對(duì)剛玉質(zhì)澆注料高溫性能的影響加入不同微粉的澆注料試樣經(jīng)1600℃熱處理后的高溫彈性模量測(cè)試結(jié)果如圖3所示。在相同溫度下,試樣的彈性模量均是隨著微粉加入量的增加而增加,常溫下,當(dāng)微粉加入量從10%增加至22%、剛玉細(xì)粉含量從18%減小到6%時(shí),澆注料彈性模量從118.31GPa增加至174.98GPa,增幅為47.9%;當(dāng)溫度升高至1400℃,試樣彈性模量隨著微粉的增加從86.63GPa增加至121.65GPa,增幅為40.4%,與圖2中的常溫抗折強(qiáng)度變化趨勢(shì)保持一致。此外,隨著溫度的升高,4組試樣彈性模量變化趨勢(shì)相同,在30~1200℃間均緩慢降低,但在1200~1500℃間急劇降低,其原因在于試樣中CA6的生成,均會(huì)增加澆注料在高溫下的顯氣孔率,從而減小其高溫彈性模量。
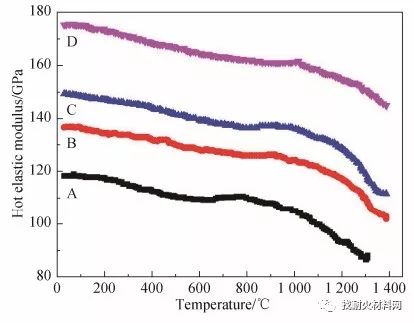
圖3 試樣的彈性模量隨溫度的變化(氧化鋁微粉含量
圖4為經(jīng)1600℃熱處理后不同氧化鋁微粉含量試樣經(jīng)3次水冷熱震后的殘余抗折強(qiáng)度和殘余強(qiáng)度保持率。由圖4可知,3次水冷熱震后,試樣的殘余抗折強(qiáng)度均在5MPa左右,變化不大,結(jié)合圖2的常溫抗折強(qiáng)度可知,氧化鋁微粉加入量越多,熱震后試樣強(qiáng)度降幅越大,表現(xiàn)為試樣的殘余抗折強(qiáng)度保持率隨著氧化鋁微粉加入量的增加而減小,其值從18.45%減小至11.97%,表明試樣的熱震穩(wěn)定性能隨著微粉含量的增加而減弱。由此可見氧化鋁微粉加入過(guò)多不利于澆注料的熱震穩(wěn)定性能,其原因在于為材料越致密,氣孔越少,吸收熱震時(shí)產(chǎn)生熱應(yīng)力的能力減弱,導(dǎo)致微粉含量高的試樣熱震穩(wěn)定性能較差。圖4 試樣3次熱震后殘余抗折強(qiáng)度和抗折強(qiáng)度保持率2.3氧化鋁微粉含量對(duì)澆注料抗渣侵蝕性能的影響經(jīng)1600℃熱處理后、不同微粉含量的試樣經(jīng)感應(yīng)爐抗渣結(jié)果如圖5所示,其中抗渣試樣可以分為3層:Ⅰ為蝕損層;Ⅱ?yàn)闈B透層;Ⅲ為原質(zhì)層。由圖5可以看出,試樣C(微粉含量18%、剛玉細(xì)粉含量為10%)的滲透層厚度明顯小于試樣A(微粉含量10%、剛玉細(xì)粉含量18%)的,試樣A和C的滲透層厚度分別為2.9和2.1mm。
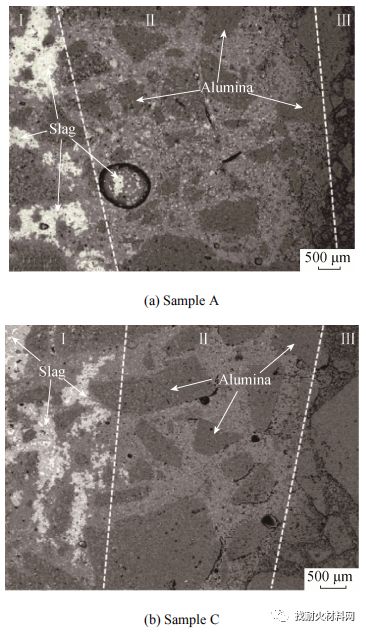
圖5 經(jīng)感應(yīng)爐抗渣后試樣的SEM照片
為研究試樣A和C滲透層厚度差異的原因,將滲透層放大,得到SEM照片,結(jié)果如圖6所示。由圖6可見,滲透層主要有白色的渣、顆粒氧化鋁和基質(zhì)組成,其中最明顯的變化為基質(zhì)中氣孔的大小和數(shù)量。澆注料試樣A(微粉含量10%)滲透層中的氣孔較大,數(shù)量較少,如圖6a所示;而加入較多氧化鋁微粉(18%)的澆注料試樣滲透層中的氣孔較小,數(shù)量較多,如圖6b所示。熔渣與耐火材料相互作用機(jī)理符合式(2)和式(3):
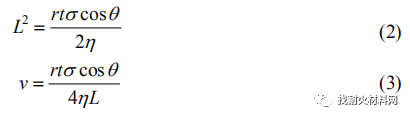
式中:L、v、θ、t、σ和η分別為渣滲透深度(cm)、滲透速度(cm/s)、熔渣與耐火材料間的潤(rùn)濕角(°)、滲透時(shí)間(s)、熔渣的表面張力(N/cm2)和滲入耐火材料中熔渣的黏度(N·s/cm2)。由式(2)和式(3)可以看出,L2與r成正比,v與r成正比,在相同的抗渣環(huán)境下,基質(zhì)中氣孔孔徑越大,渣的滲透深度越大,渣滲透速率越快,試樣C的抗渣侵蝕性能要優(yōu)于試樣A,即氧化鋁微粉含量的提高有利于增強(qiáng)澆注料的抗渣侵蝕性能。

圖6 試樣經(jīng)抗渣試驗(yàn)后滲透層的SEM照片
除了氣孔影響試樣抗渣性能外,CA6形貌也能對(duì)澆注料的抗渣性能產(chǎn)生較大的影響。圖7為試樣經(jīng)抗渣后滲透層和原質(zhì)層交界面的SEM照片。圖7a和圖7b分別為試樣A(微粉含量10%)和試樣C(微粉含量18%)中渣從滲透層、侵蝕層到原質(zhì)層的SEM照片。由圖7a和圖7b可以看出。試樣A的侵蝕較C嚴(yán)重。將2個(gè)試樣的反應(yīng)界面層放大,得到試樣圖7c~圖7f,分別對(duì)應(yīng)試樣A和試樣C。對(duì)比圖7c和圖7d可知,試樣A的基質(zhì)結(jié)構(gòu)較為疏松,不利于抗熔渣的侵蝕;而試樣C的基質(zhì)結(jié)合緊密,渣不容易滲透和侵蝕。進(jìn)一步放大原質(zhì)層得到圖7e和圖7f,可見,加入較少微粉的試樣A中CA6成等軸狀,基質(zhì)結(jié)合疏松;而加入較多微粉的試樣C中CA6呈板片狀,穿插結(jié)合,使基質(zhì)結(jié)合更加致密。
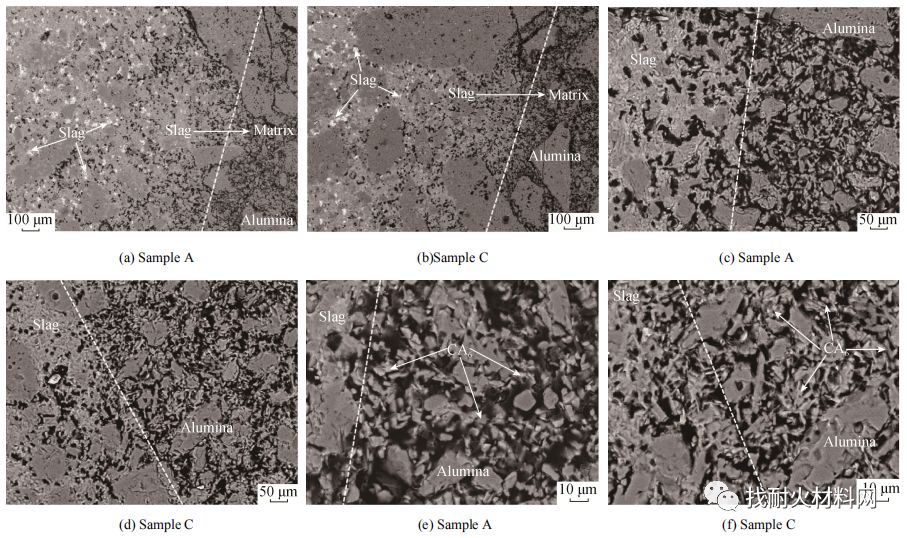
圖7 試樣的侵蝕層和原質(zhì)層交界面的SEM照片
1) 隨著氧化鋁微粉含量的增加和剛玉細(xì)粉含量的減少,經(jīng)不同溫度熱處理后澆注料試樣的常溫性能和高溫性能均有不同程度的提升,經(jīng)1600℃處理后的試樣常溫抗折強(qiáng)度、常溫彈性模量和在1400℃時(shí)彈性模量可分別提高53.9%、47.9%和40.4%。2) 微粉加入過(guò)多不利于澆注料的熱震穩(wěn)定性。氧化鋁微粉加入量越多,熱震后試樣的殘余抗折強(qiáng)度保持率隨著氧化鋁微粉加入量的增加而減小,在3次水冷熱震后材料的殘余抗折強(qiáng)度保持率從18.45%減小至11.97%。3)隨著加入氧化鋁微粉含量的增加,澆注料的抗渣侵蝕性能逐漸提高,滲透層厚度從2.9mm減小至2.1mm,其由于較高含量的微粉會(huì)使?jié)沧⒘系臍饪卓讖阶冃。龠M(jìn)了原質(zhì)層中板片狀CA6的穿插結(jié)合,基質(zhì)結(jié)合更加緊密,有利于澆注料抗渣性能的改善。